What is the origin of the International Year of Glass?
For more than 60 years, the United Nations General Assembly has proclaimed the United Nations International Year to recognize international cooperation and concerted efforts in important fields and the contributions made by relevant organizations and institutions to society, such as the International Year of Astronomy (2009), the International Year of Chemistry (2011), International Year of Light and Light-Based Technologies (2015), International Year of the Periodic Table of Chemical Elements (2019), etc. The International Year of Glass in 2022 is the first time the United Nations has named a year after a single material. The initiative to establish the United Nations International Year of Glass is led by the International Glass Association and has received positive response and support from the global glass academia and industry. As far as we know, universities, research institutes, associations, museums, and glass companies from 90 countries and regions on five continents have provided more than 2,100 letters of support for the International Year of Glass initiative. Among them, the China Silicate Society took the lead in organizing Nearly 200 letters of support from relevant domestic units. On May 18, 2021, at the 66th plenary session of the 75th United Nations General Assembly, 2022 was officially approved as the United Nations International Year of Glass.
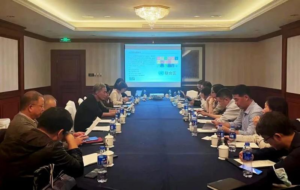
What is the significance of the establishment of the International Year of Glass by the United Nations? Glass is one of the earliest man-made materials invented by human beings. It has been used in human life for thousands of years. From Mesopotamia 4,000 years ago to the remains of ancient Egypt, there were small Unarthed glass beads. Nowadays, with the rapid improvement of the level of science and technology, it is widely used in construction, communication, transportation, life and health, new energy, aerospace, art, and other fields. It is a very important material in daily life and high-tech fields. played an important role in the history of technological inventions. For example, glass optical fibers have brought about a paradigm change and triggered a global communications revolution; the development of glass optics and optoelectronics has expanded human understanding of the universe; glass panels support solar cells and provide clean energy; glass fibers strengthen wind power generation Blades, which reduce carbon emissions; touch-sensitive glass screens bring smartphones into people’s lives; bioglass enables muscle tissue design and regeneration, and can solve hearing and dental problems; vitrification of hazardous waste improves the safety of nuclear energy Sex, etc… This transparent enabling material not only enters thousands of households and becomes an important medium for art, but also supports the development of many technologies. Its history is connected with the history of mankind. The establishment of this year of glass highlights the indispensable and important position of glass in many fields such as science and technology, economy, environment, culture, and society, and its role in addressing the challenges of a sustainable society, building an inclusive society, and achieving global economic recovery, promoting the development of emerging technologies, etc., are conducive to promoting the construction of a global glass community, serving the multilateral governance system with the United Nations as the core, and further highlighting the importance of glass to science, technology, economy, and sustainable development and the importance of glass to human civilization. and artistic contributions.
What are the important activities of the United Nations International Year of Glass in China?
The Organizing Committee of the International Year of Glass has been divided into 18 regional committees according to various regions. Among them, China, Germany, and Brazil are independent regional committees, and the China Silicate Society is the leading unit of the regional committees in China. We will actively respond to the relevant resolutions of the United Nations, give strong support to the International Glass Association, and organize various activities of the International Year of Glass in China, including the 32nd China International Glass Industry Technology Exhibition, the 10th International Advanced Glass Symposium, the China Function Glass Academic Symposium and Forum on New Optoelectronic Materials, Summit Forum on Glass and Human Civilization, “One Belt, One Road” International Glass Art Exhibition, Glass Popular Science Series Activities, Glass Museum Series Activities, Glass Themed Winter Camp, etc.
From February 10th to 11th, it officially opened at the Palais des Nations, the European headquarters of the United Nations in Geneva, Switzerland. At present, we plan to hold the launching ceremony of the United Nations International Year of Glass in China and the “Glass and Human Civilization” summit forum in Beijing in April and announce the selected propaganda slogan. The 32nd China International Glass Industry Technology Exhibition (referred to as China Glass Exhibition) to be held in Shanghai this year is one of the important events of the United Nations International Year of Glass (originally scheduled to be held from April 13 to 16, due to the epidemic prevention and control in Shanghai. The same heavyweight international events include the “National Glass Day” event in the United States, the theme event “From Pharaoh to High-Tech Glass” in Egypt, the 26th International Glass Conference in Germany, and the closing of the International Year of Glass in Japan at the end of the year. formula, etc.
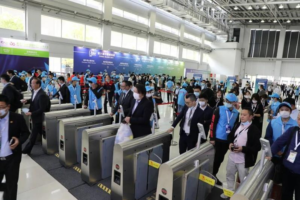
China Glass Exhibition
This year’s China Glass Exhibition is still sponsored by the China Silicate Society and undertaken by Beijing China Silicon Exhibition Co., Ltd. The exhibition area planning will be basically the same as the previous one: Hall E1 is the international exhibition area, which brings together German and Italian national pavilions and many global glass industries. Mainstream brands, Hall E2 is for original film manufacturers and large-scale comprehensive glass manufacturers, Halls E3 to E6 are for deep processing equipment manufacturers, Hall E7 is a non-equipment exhibition area, and a special area for art glass and daily-use glass is set up.”Popular science” is also a focus of the International Year of Glass in China. In addition to planning to set up a special area for popular science at the China Glass Exhibition, we will also organize “Science and Technology Activity Week” and “National Science Popularization Day” in May, June, and September. , for middle school students and college students, adopt various forms to publicize glass science; in July and August, a series of activities for primary and middle school students to enter the glass museum and themed cultural center will be carried out. In addition, the International Year of Glass academic issue of “Journal of Silicate” sponsored by the China Silicate Society has been published, including 18 review articles and 13 research articles, which introduce the preparation technology, structural characterization, and application exploration of glass in detail. It is also a gift from Chinese glass technology workers for the International Year of Glass.